Texaa is a family business employing around fifty people in one of greater Bordeaux’s activity centres in a building designed by architects Luc Arsène-Henry and Alain Triaud. Come into the lobby, follow a narrow corridor, push open a sound-proofed door with a round window in it and you are in the workshop.
Workshop Tour
Since its foundation in 1978, Texaa has remained attached to a mix of craftsmanship and semi-industrial activity. There is no doubt that it is one of the only acoustic solutions brands to be in full control of manufacturing from receiving reels of yarn right through to conditioning products for dispatch. The workshop’s large open space accommodates the knitting of our sound-transparent fabric Aeria, which covers all Texaa products and the manufacturing of those very products: Stereo panels, Strato breathing ceilings, Abso accessories, Vibrasto cladding, curtains and blinds. Most of our employees are trained seamstresses or technicians trained by Texaa, and have worked here for several years, even decades. Everyone has his or her own expertise and knows the jobs of others, so they can help out when orders flood in.
All the production steps are manual. In the knitting area, 300 reels of yarn are positioned on the rather old, weird-looking machine that we call the creel. The yarn is cleared and if it breaks, it is skillfully tied with a sheet bend, the only knot that produces no unsightly defect in the finished fabric. Each yarn is then introduced into the latest-generation knitting machine that will produce the velvety grain of the Maille Ronde or the delicate net of the Grande Maille Ronde. Even in a very open mesh, the thread does not break; it is surprisingly strong. Really effective solutions can be manufactured with knitted yarn! Texaa invested in modern knitting machines to safeguard production and ensure quality of the knitted fabrics.
In the product area of the workshop, our seamstresses turn components into actual merchandise, and also add zippers or tapes onto sound-absorbing curtains. For Abso products, covers are tightly stretched around blocks of foam at the right tension to form wrinkle-freeshapes. Stereo or Strato frames are rivetted together with a pneumatic gun. The absorbent material used to make the slats of our blinds is glued, using a special machine developed by Texaa. Vibrasto installation battens are covered by hand. Everyone is concentrated, no unneeded movements and the necessary coordination is maintained, because each workstation depends on the others.
Texaa manufactures its products and this is obviously a great advantage: time and materials, finished quality and tailor-made projects are all under control. Architect Daniel Rubin says that the Texaa workshop makes you “feel like
playing” in a real exchange with the teams. Manufacturing is not cut off from the other skills in the organisation. The engineers in product development pursue new ideas in close collaboration with practices and requests. Every
acoustic solution represents a complex balance between regulatory requirements, technical performance and impeccable finishing. Texaa solutions are easily installed and dismantled and always leave great freedom for architects.
At its own scale, Texaa manufactures products that last and works with suppliers, who are not on the other side of the world, like it always has with an essential focus on quality.
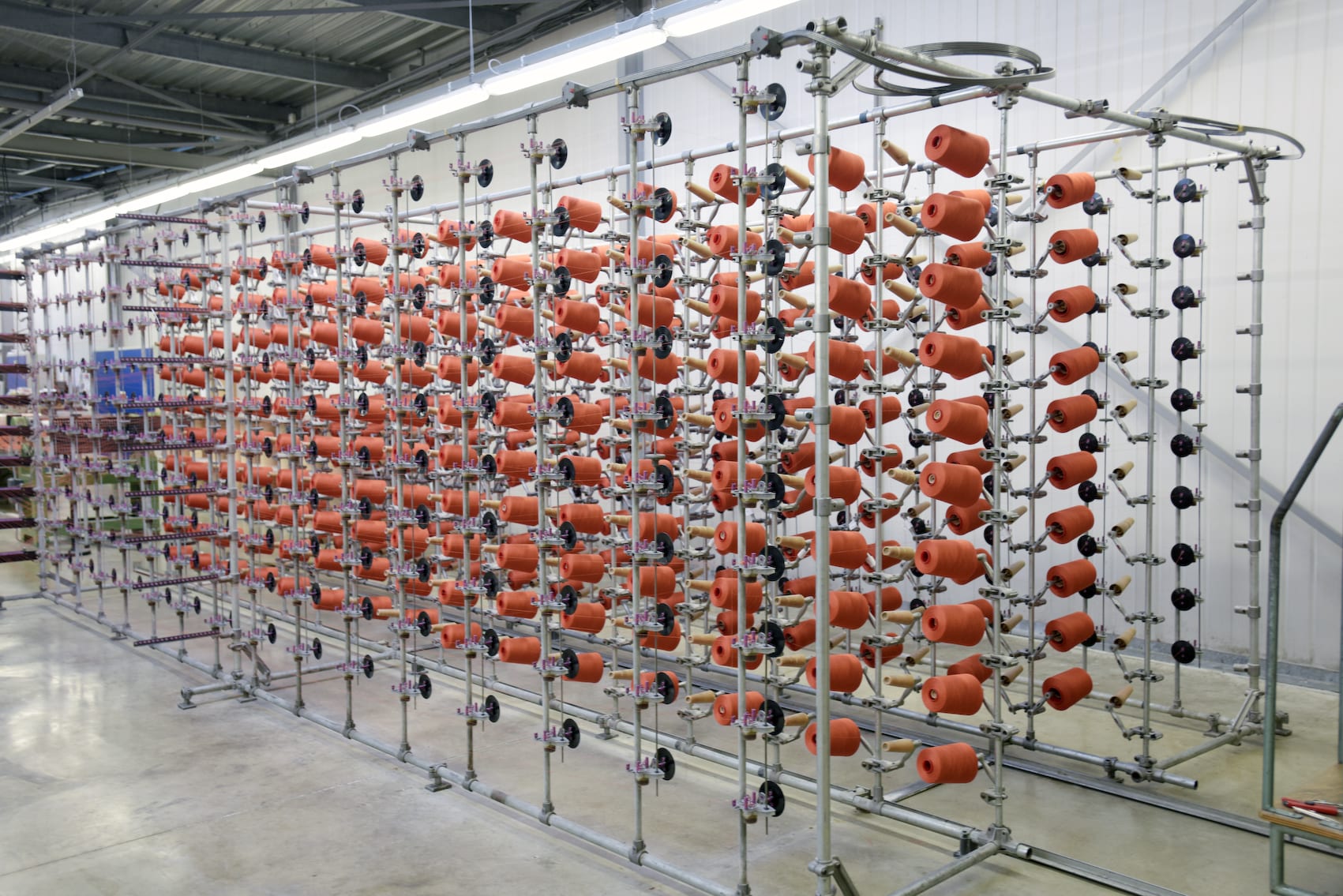
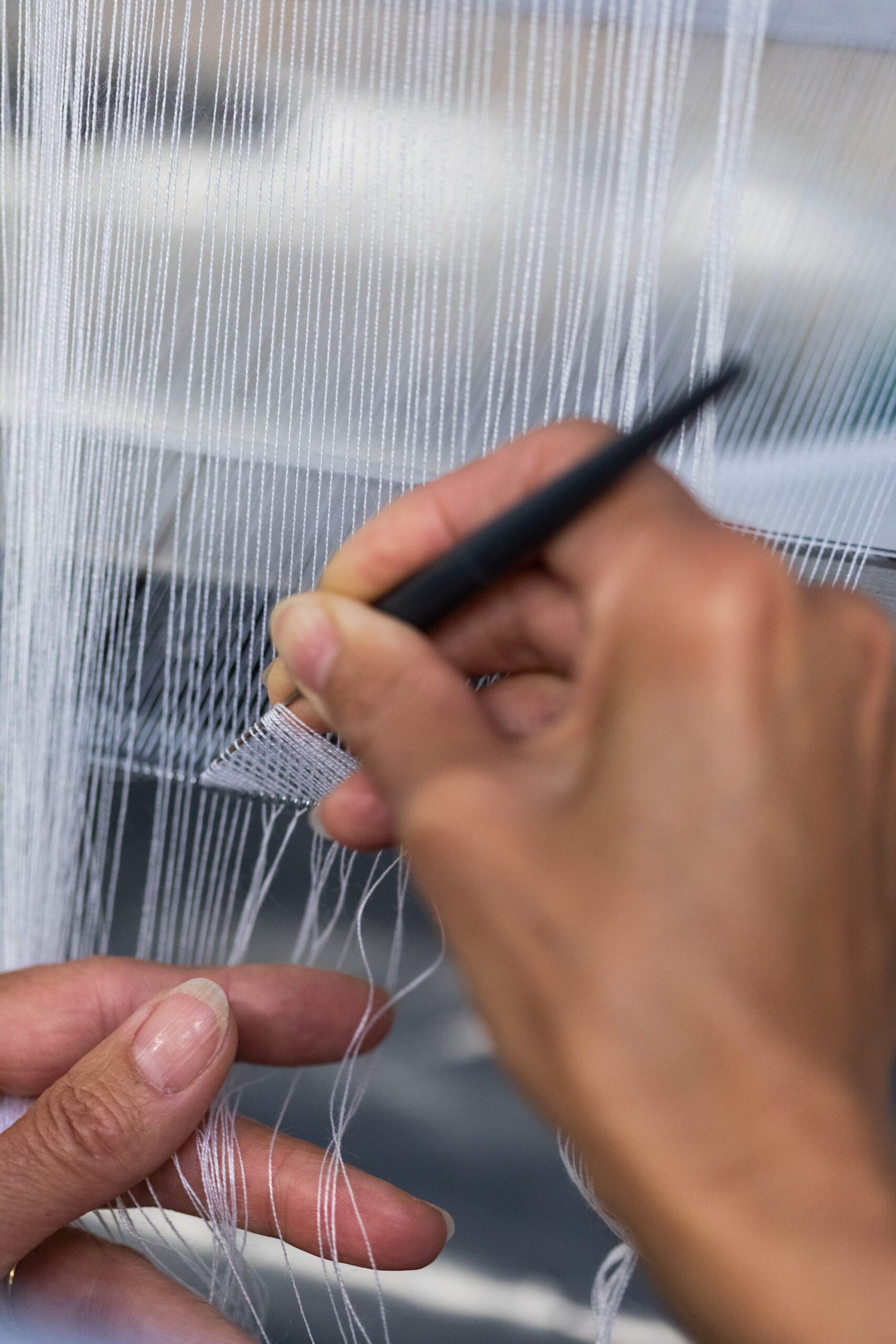
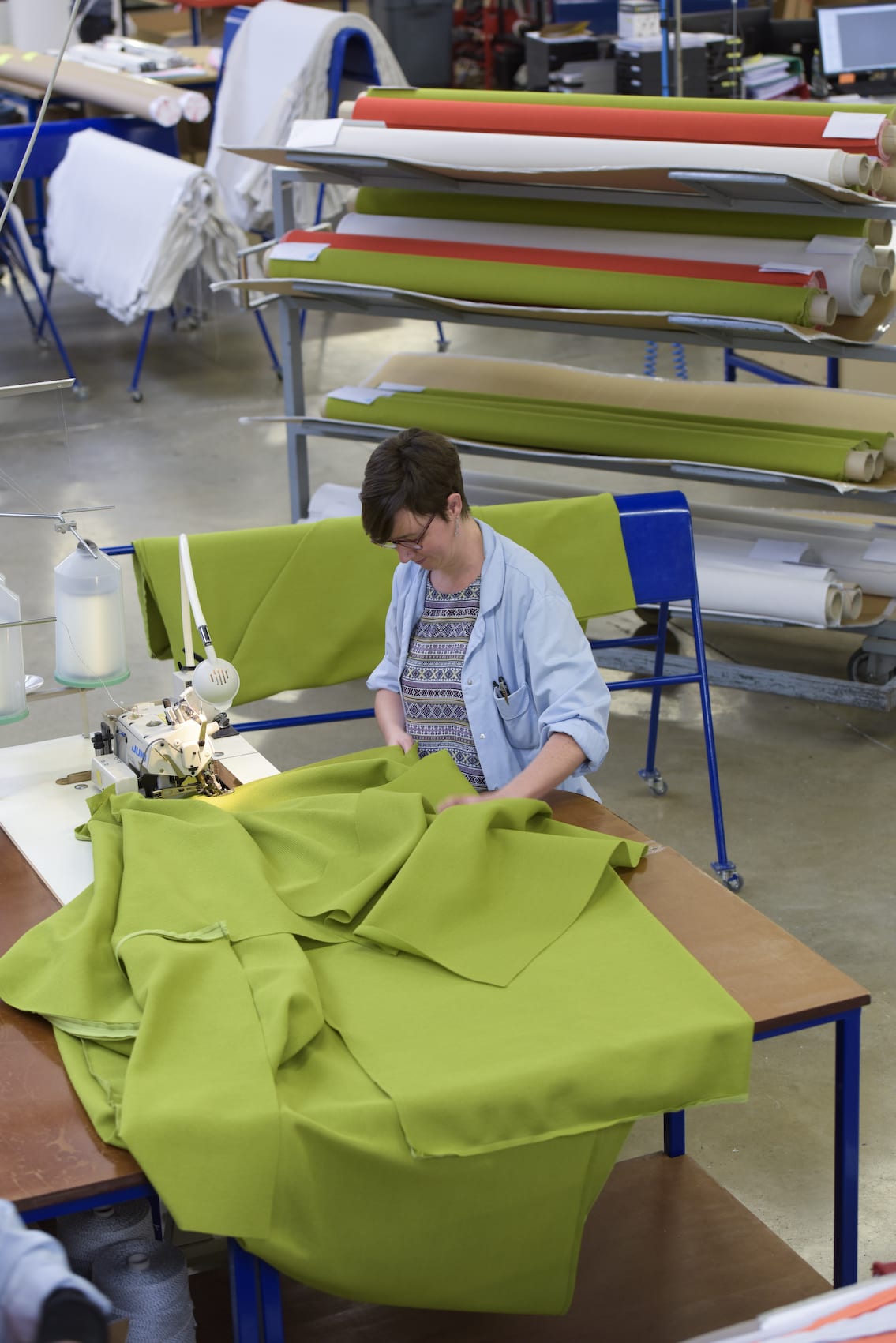
How can I get a quote?
By contacting the Texaa business representative of your region by telephone or e-mail and leaving your contact details and what you need. We will send you a quote promptly.
How can I order Texaa products?
Our products are manufactured in our workshop and made available to order. Just contact the Texaa business representative of your region. If you already have a quote, you can also contact the person handling your order: the name is at the top left of your quote.
How do I get my products installed?
Joiners and upholsterers are the best skilled to install our products easily. We work regularly with some professionals, who we can recommend. If you have a tradesperson, who you trust, we can support him/her. You can find our installation instructions and tips here.
Got a technical question?
All our technical data sheets are here. Your regional Texaa business representative can also help; please feel free to contact him/her.
Can I have an appointment?
Our business representatives travel every day to installation sites and to see our customers. Please feel free to contact them and suggest the best dates and times for you, preferably by e-mail.
Lead times
Our products are manufactured to order. Our standard manufacturing time is 3 weeks for most of our products. Non-standard products take from 5 weeks. We also perform miracles on a regular basis! Please feel free to contact us.
Who should I call?
To get a quote, a delivery time or technical information, we recommend you call your regional Texaa business representative, who you can find here.
Order tracking
If you need information about your order, please contact the person in charge of handling it: the name is at the top left of your quote.