The work consisted of taking down a hundred Stereo panels installed in the old group headquarters, removing their covers, changing their fixing systems, putting new covers back on them, and finally reinstalling them in the new premises, located a few kilometres away. Everything had to be done in record time. This was the challenge that CFAO Group set for Texaa, when it moved. This story of a major reuse operation was a success thanks to products designed to last, as well as to the commitment of all the stakeholders.
CFAO headquarters, an example of reuse
2,303.5 kg of CO2 saved by using 111 restoration kits instead of manufacturing new panels!
111 refurbished panels represent:
- 111 metal frames and 111 pieces of sound-absorbing felt saved to manufacture new panels
- Half the quantity of packaging used
- A reduction of 18.55 kg CO2/m² , including 1.4 CO2/m² from the avoidance of component and finished product transport emissions.
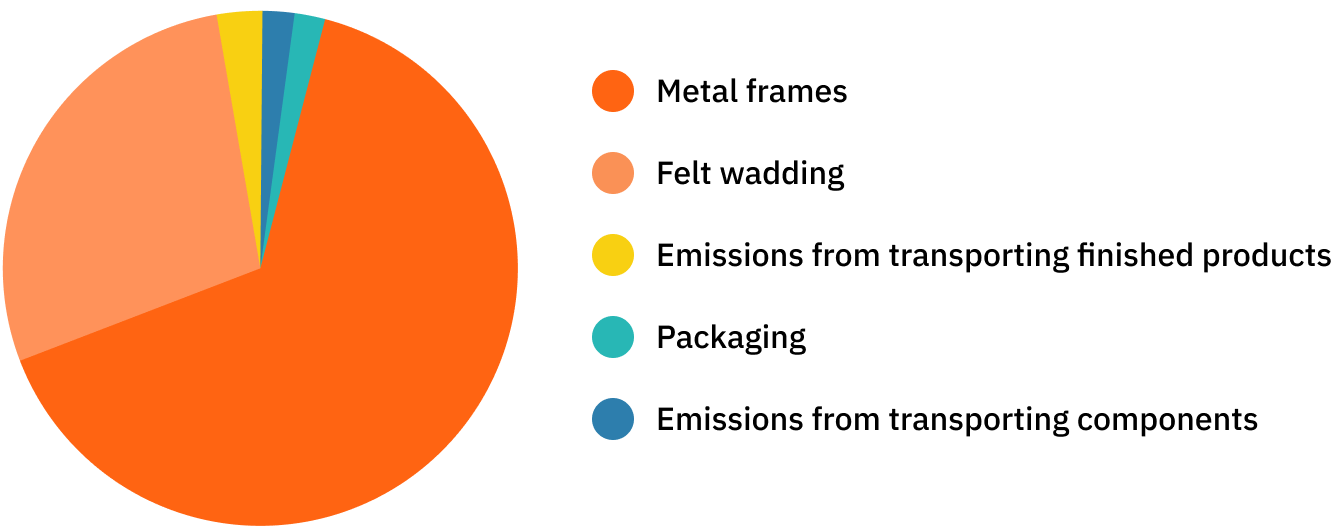
A straightforward question, or apparently so…
“In 2013,” explains Bruno Mallet, CFAO’s real estate and general services manager, “we modified the offices of our old head office into an open space area. The acoustics therefore became challenging. At that time we called in Texaa, whose products I was familiar with. I had noticed how effective they are when installed, when I used to work at the Équipe newspaper.” So almost a hundred Stereo panels were fitted to the walls or suspended in baffles. Nine years later, when the group decided to leave its premises in Sèvres to move to a more modern building in Boulogne-Billancourt, Bruno Mallet contacted Texaa again with an apparently straightforward question: can you move the panels and adapt them to a new spatial arrangement with a fresh decorative design? “We had adopted a recycling approach,” he continues. “We had purchased the furniture and partitions of the previous occupant. Reusing the panels was also part of the idea. Furthermore, buying them was a big investment, but a sustainable one. The panels had originally met our requirement, had not deteriorated, and we had encountered no problem in their use. In very practical terms we had no reason, other than a financial one, to get rid of them.” So, it was just a question of implementing this ambitious project, identifying and quantifying what was needed, then planning installation, so that onsite work could run smoothly. The most important thing was to find the right work method, because, as well, time was of the essence. The whole job, of which reusing the panels was just one very small part, and the move had to be finished in three months with a restricted budget.
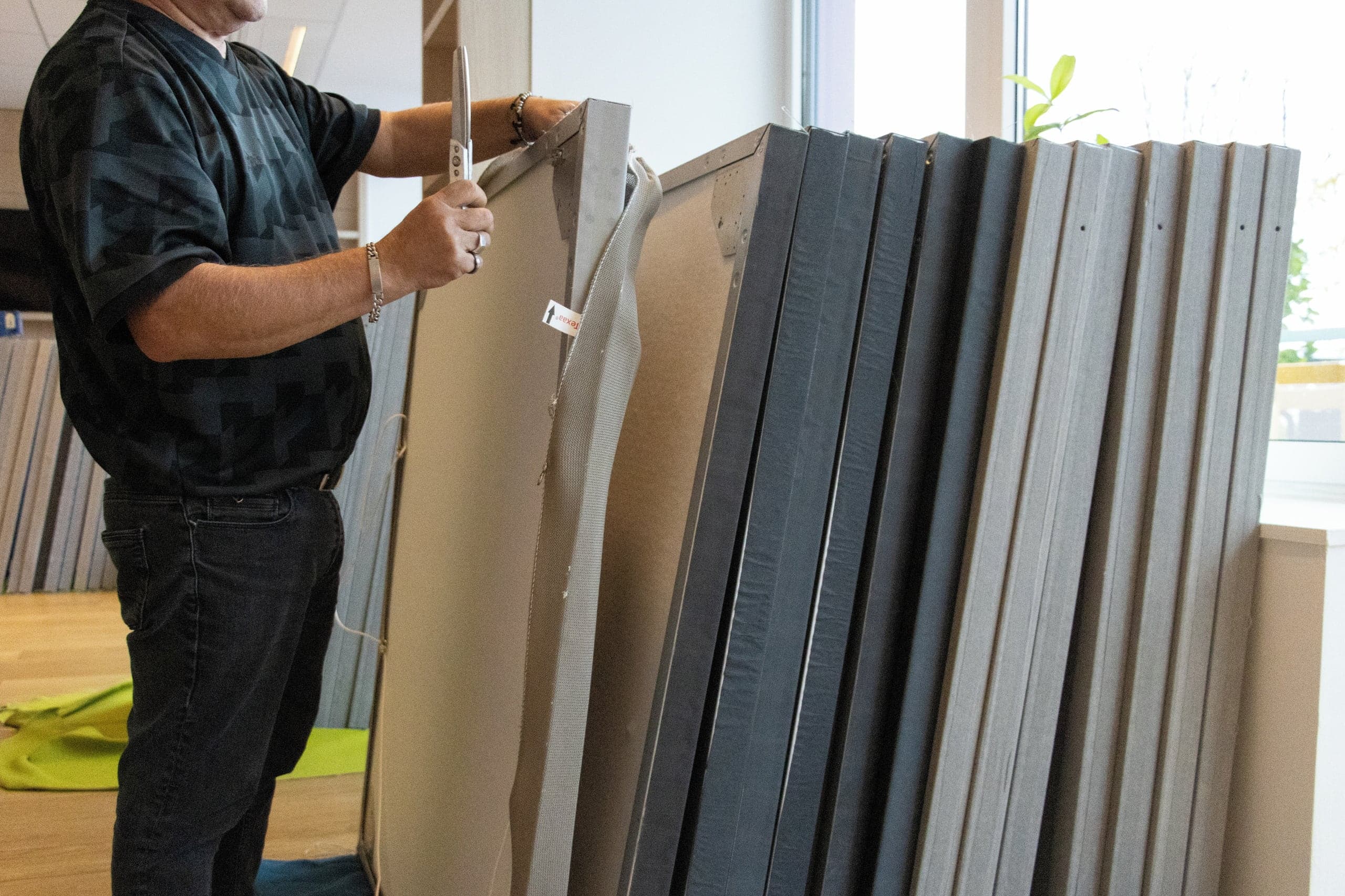
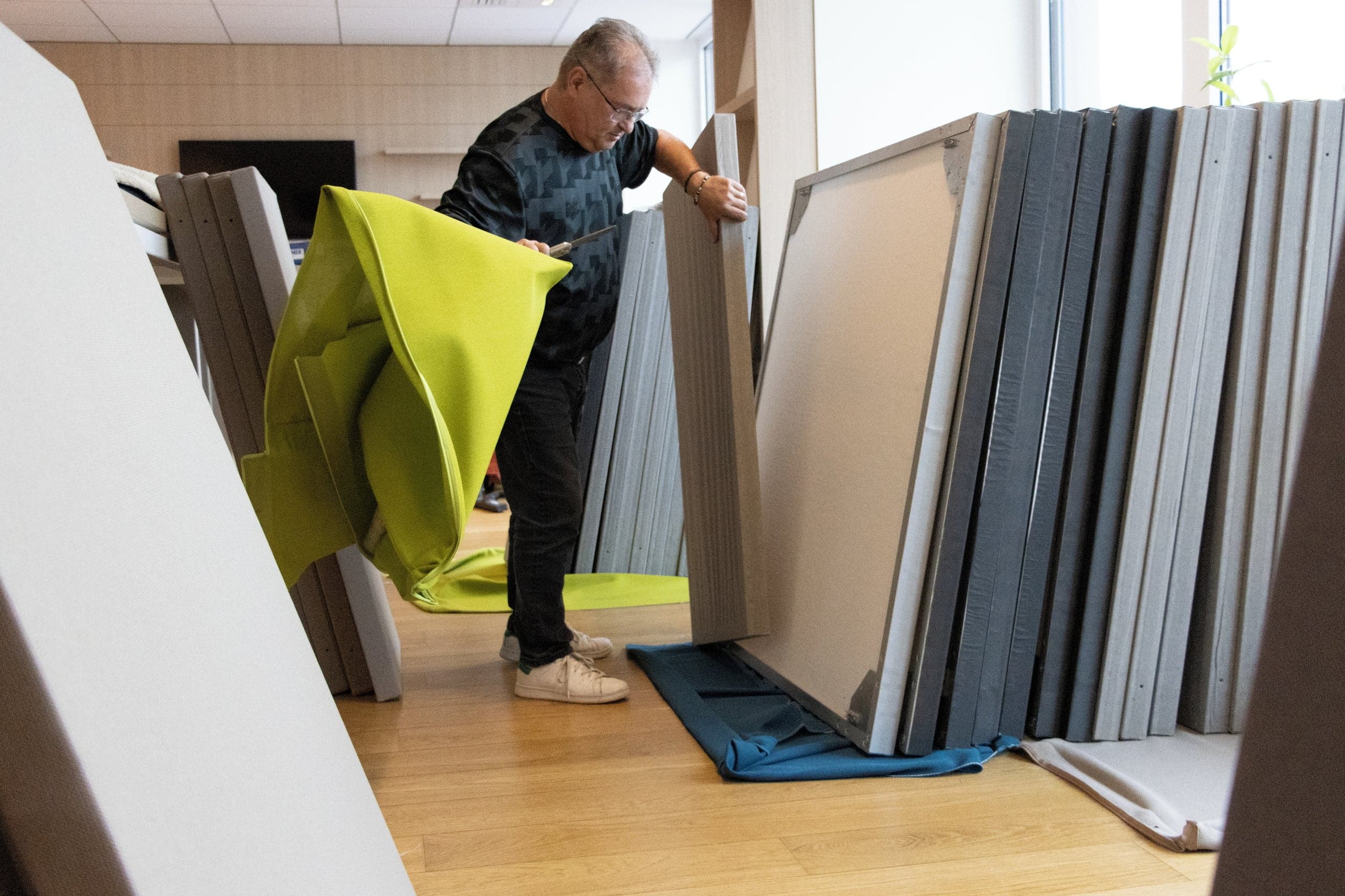
Renovation operation
Bruno Mallet points out: “Without a salesperson, who was enthusiastic about the solution I wanted to implement, to support me, it would never have worked. Sophie [Tagachoucht of Texaa’s sale team, Editor’s note] immediately bought into the project and set up a system to monitor it from start to finish. There was real trust in the relationship, and this enabled the Texaa team to work on site unsupervised. This was very important for me.” Step one: choose the new colours, find the right combinations to produce a well-balanced, welcoming result. Step two: work out how the panels would be arranged to be able to calculate the number of replacement covers, and specify the new fixing systems, so that everything would be ready for the renovation. The number of new panels necessary also needed to be calculated, which turned out to be around thirty, in addition to the reconditioned ones. Step three: get organised. The panels in the previous premises were taken down, while people were still working in them, before they moved. The cafeteria of the new headquarters was made available for the team of installers led by Pascal Cauvin, where they set up a temporary workshop with more sophisticated tools than usual, including a compressed air machine from Texaa’s workshop outside Bordeaux, to make changing fixing systems easier. There was even a small coffee machine. “I’ve worked with Texaa for more than twenty years,” says Pascal. “We often change covers, but this was the first time we were doing it at this scale. Same thing for the fixing systems. It enabled us to learn a lot more about the jobs in the workshop. We could almost work there ourselves! On the CFAO job, we did all the operations.” He adds, “It’s also the first time we installed panels like pictures on hanging rails. They look really striking”. And once all the panels were up, you couldn’t tell the difference between the reconditioned panels and the new ones.” All the panels were installed at the new site in just three weeks. On schedule! What’s more, this high volume operation enabled Texaa’s teams to learn a lot, both in logistics (panel removal, renovation, reinstallation and storage etc.) and around design and how products evolve. The system used to close covers on the panels, for example, has since been improved. And nearly all the newer Stereo fixing systems can be adapted to older models.
A new stage
“Texaa has always carried out renovation operations on site, for example reconditioning panels and recovering them with new Aeria fabric covers,” explains Matthieu Demptos, CEO of Texaa. “But this project enabled us to go much further and to learn a lot, because we were able to test out how are solutions might be recycled on a large scale. This is an important part of our environmental policy to reduce the carbon footprint of our business and our products. It is true that Texaa products are made to last. Their shapes and their colours are designed not to go out of fashion. The materials they are made of, including steel, sound absorbing felt and the Aeria fabric, have long useful lives far beyond those of standard products.” To make the products last longer and thereby consume less raw materials, they have to be traced to be able to be recovered, reused or reconditioned. This is often very complicated, but here all the conditions were right. Even the logistics couldn’t have had a lower impact, because we installed a temporary workshop on site, and the two premises were only a few kilometres apart. “We had the right partners”, continues Matthieu. “A hands-on customer, who made the order, a very highly qualified installer, and a very specially motivated team. This is the perfect case study that really highlights the quality of what can be done with renovation. And it’s even more evidence for what we hope to show, namely that a Stereo panel never needs to be thrown away.”
Project name: CFAO
Year to be delivered: 2022
Town-city / Country: Boulogne-Billancourt, France
Project owner or contracting authority: CFAO Group
Photographer: Hervé Abbadie
How can I get a quote?
By contacting the Texaa business representative of your region by telephone or e-mail and leaving your contact details and what you need. We will send you a quote promptly.
How can I order Texaa products?
Our products are manufactured in our workshop and made available to order. Just contact the Texaa business representative of your region. If you already have a quote, you can also contact the person handling your order: the name is at the top left of your quote.
How do I get my products installed?
Joiners and upholsterers are the best skilled to install our products easily. We work regularly with some professionals, who we can recommend. If you have a tradesperson, who you trust, we can support him/her. You can find our installation instructions and tips here.
Got a technical question?
All our technical data sheets are here. Your regional Texaa business representative can also help; please feel free to contact him/her.
Can I have an appointment?
Our business representatives travel every day to installation sites and to see our customers. Please feel free to contact them and suggest the best dates and times for you, preferably by e-mail.
Lead times
Our products are manufactured to order. Our standard manufacturing time is 3 weeks for most of our products. Non-standard products take from 5 weeks. We also perform miracles on a regular basis! Please feel free to contact us.
Who should I call?
To get a quote, a delivery time or technical information, we recommend you call your regional Texaa business representative, who you can find here.
Order tracking
If you need information about your order, please contact the person in charge of handling it: the name is at the top left of your quote.