Two giant bubbles, in yellow and white, the colours of arc en rêve. Each with a surface area of two hundred and twenty-eight square metres and some seven metres high…
Acoustic sails
for an inflatable,
arc en rêve
centre d’architecture
A work by Hans-Walter Müller
Hans-Walter Müller is a pioneer of inflatable art and creates plastic bubbles inflated with pressurised air. Since the 1960s, he has created dozens of such structures, for theatres or exhibitions, including a
200 seat church weighing no more than 39 kg. “An inflatable” he explains “is simply a skin containing a space, separating the outside from the inside, appearing and disappearing and sometimes dematerialising.
It’s an unfamiliar type of space, full of fun and fantasy, a far throw from traditional buildings…You can create huge constructions using very little energy at all.” 1
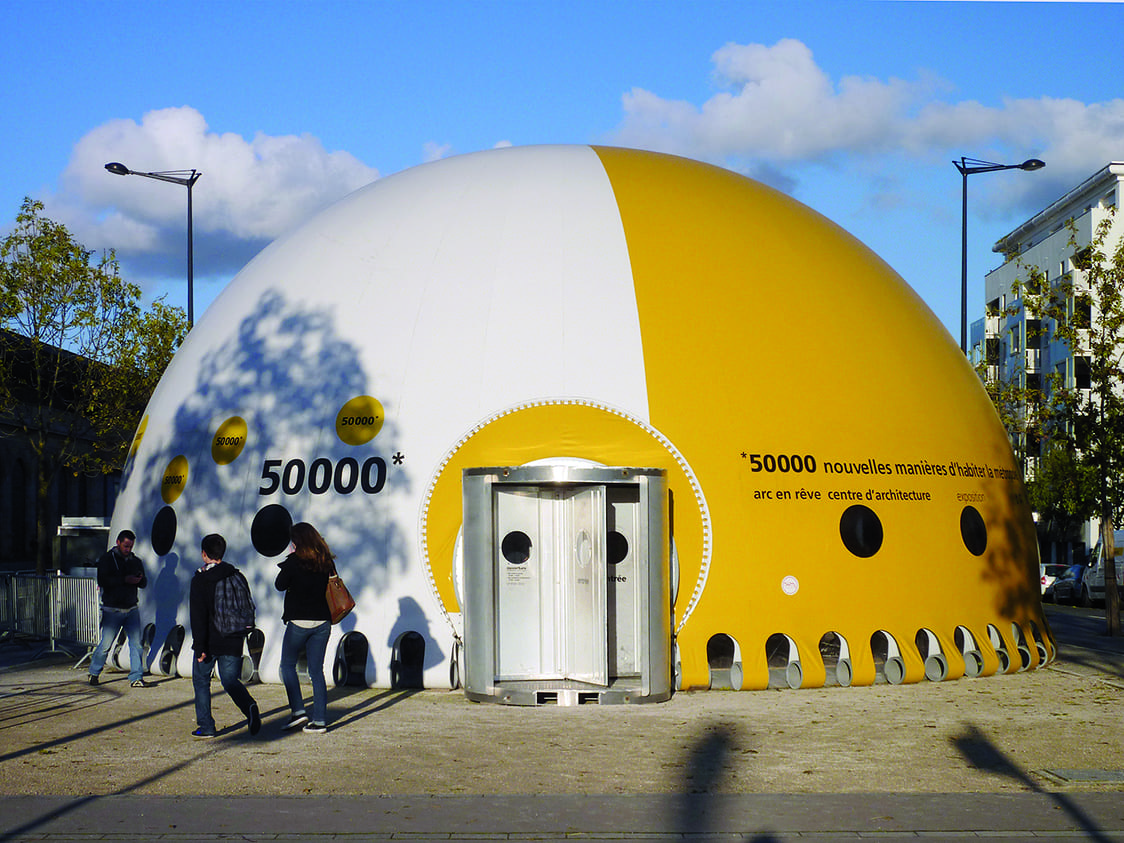
A nomadic exhibition space
Hans-Walter Müller was commissioned to create this structure by arc en rêve in 2012, as part of an exhibition initiated by the Bordeaux urban community presenting “50,000 new homes.” Arc en rêve wanted a nomadic exhibition space which would be lightweight, easy to transport and put up, original enough to arouse the local inhabitants’ interest and which could then be taken down in no time at all, before moving on to a new site, leaving without a trace. Hans-Walter Müller’s project fitted these desiderata perfectly. Not only does the bubble provide a functional, multi-purpose exhibition space, but it is also a handsome object from the aesthetic point of view, with its bright colours and inimitable style.
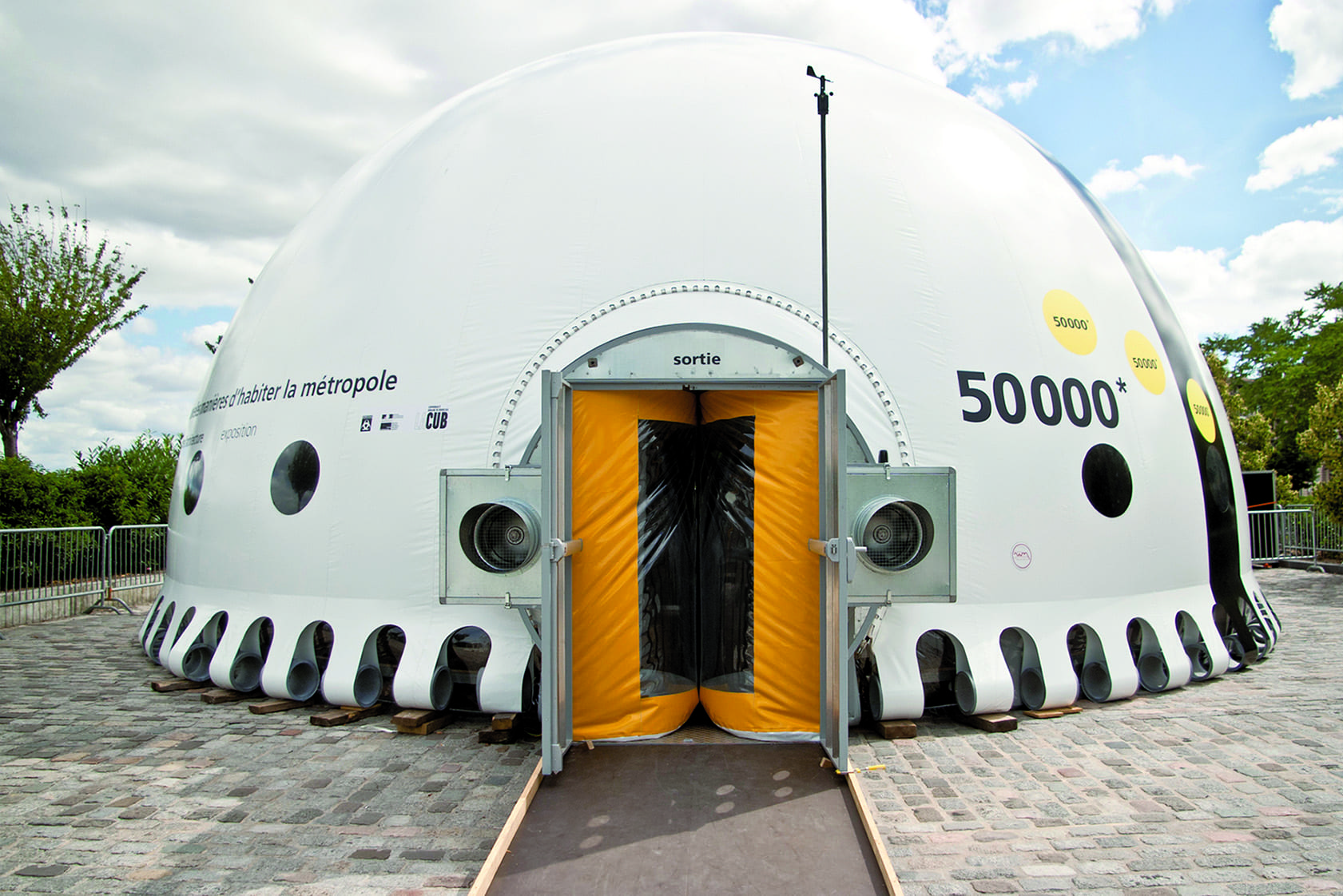
Acoustic comfort
As the inflatable is formed by two symmetrical semi-circular domes, its acoustics are particularly resonant. “Any building shaped like that would be terribly prone to echo”, Fabrice Lalanne explains.
He oversaw Texaa’s involvement in the project. “The most surprising acoustic effects are generated”, he goes on. “If you stand in a precise spot, you can hear a conversation being held exactly opposite with perfect clarity, but you can’t make out what your nearest neighbour is saying. Sound transmission phenomena such as these have been well documented down the centuries, and were deliberately used in days gone by to communicate with people suffering from contagious diseases. The vaulted halls of some hospices, for example, enabled people to communicate with the sick without getting too close, as their voices were carried along the walls.” If the inflatable was to be used as an exhibition space, this was not necessarily too serious a problem, but if it was also to serve as a place for conferences and public debate, then something had to be done… but what? There was no ceiling to clad with sound absorbing materials, no structural framework from which to hang large acoustic objects. A number of objects from the Abso range (totems, cushions, etc.) were tried, with an aim to disrupting the sound waves travelling parallel to the inflatable’s walls. Texaa also turned to Christian Malcurt, a specialist in concert hall acoustics, for his expert opinion. Some means had to be found of placing obstacles inside the inflatable’s volume, in order to fragment the space. What about using fabric hangings or velum?
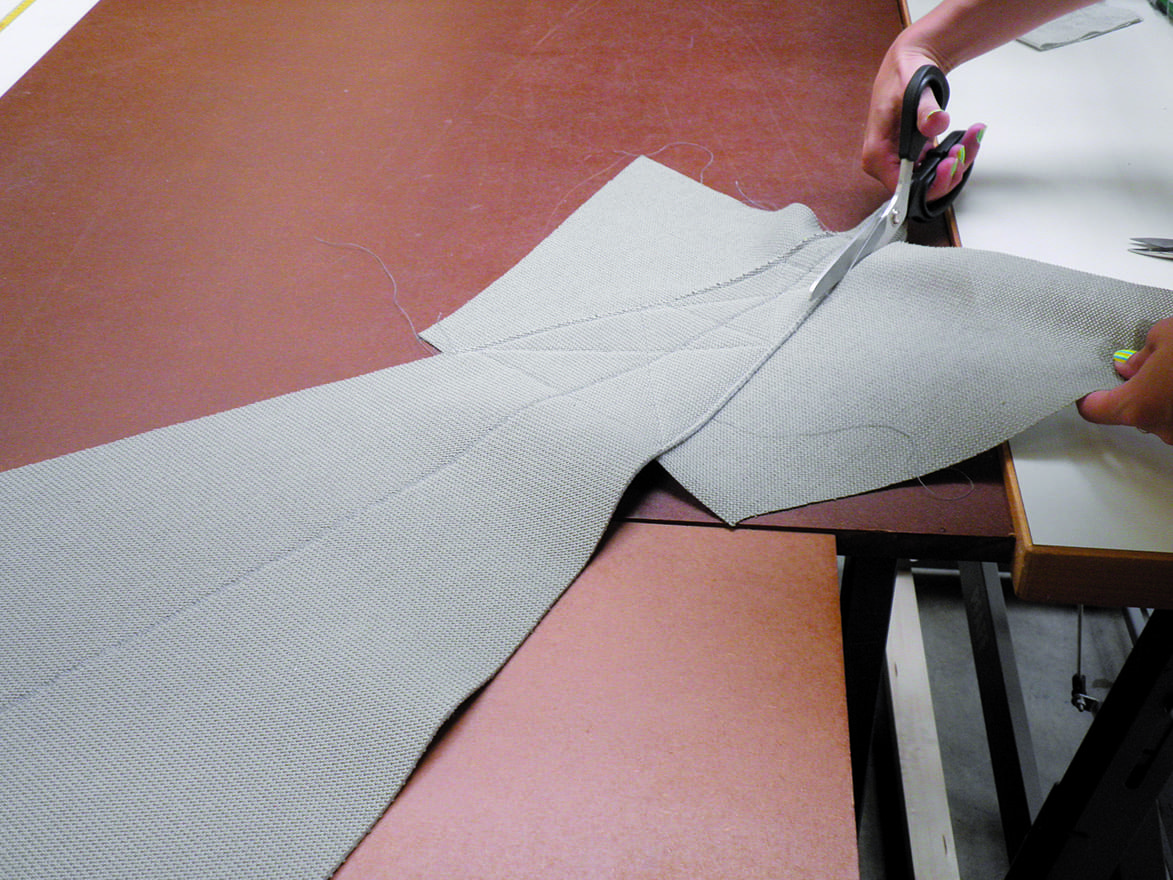
“I think we should go for triangular sails”, Michel Jacques decided.
“That way we will be able to play freely with the fullness of the available space, while still preserving a sense of volume…”
“The sails were made to measure, just like our blinds”, Edwige Carnis, head of the sewing department at Texaa®, explains. “But in this case we used Vibrasto 03 with a layer of Aeria on each side. The most complicated part of the whole process was finding the best way of assembling the multiple layers in each sail. For example, what type of stitch should be used so that they held together but would still look good on both sides. In the end we used a zigzag. The two edges were simply sewn together, with no overlap. The reinforced finishing required at each corner gave us no undue cause for concern, because we use the same technique for the cubes in the Abso range.”
Once the acoustic performance of the sails had been tested in laboratory conditions, it was time to try them inside the inflatable to check their performance and make sure the hanging system worked. It was important that the resulting effect be easy not only on the ear, but also on the eye… The sails were unfolded and anchored into place at fastening points fixed to the walls of the inflatable with high-frequency welding. Hans-Walter Müller is a past master in this technique. “When I first started making inflatables” he explains, “I used the cheapest materials available and a roll of sellotape. I remember how I used to stick two 50 m lengths together by sellotaping down the join as I moved progressively backwards. That way I could only see the part I had completed, and not what remained to be done! When I first showed my work to the public, some people couldn’t see past the sellotape. They used to call me ‘Müller the Sellotape Man’. Nowadays, I’ve given up on the sellotape and use high-frequency welding instead. So now they call me ‘Müller the Welder.’ And when one considers the strain his soldered joints are capable of withstanding, it’s clear to see that, at the age of almost 80, Mr Müller is no amateur…
Once in place, the “acoustic sails” literally float in the air, their gentle curves espousing the arc of each semi-circular sphere, in a play of light, colour and shade. However simple, their level of acoustic performance is high, and the improved level of resonance immediately perceptible. This was quite obvious when one went from the first space, where three sails had already been set in place, to the second where nothing had yet been done… Could an improvised experiment of this nature in an atypical space be of any use in the treatment of more conventional volumes?
“This whole adventure was a bit of a challenge for us”, Fabrice Lalanne concludes. “There’s a great deal of pleasure to be had in hunting down solutions for the acoustics of unique spaces—it’s the sort of trial and error process that makes you think and helps you progress. And it also has to be said that this inflatable is a particular favourite of mine!”
1 in. Techniques et architectures nº 304, 1975, pp. 73-74
How can I get a quote?
By contacting the Texaa business representative of your region by telephone or e-mail and leaving your contact details and what you need. We will send you a quote promptly.
How can I order Texaa products?
Our products are manufactured in our workshop and made available to order. Just contact the Texaa business representative of your region. If you already have a quote, you can also contact the person handling your order: the name is at the top left of your quote.
How do I get my products installed?
Joiners and upholsterers are the best skilled to install our products easily. We work regularly with some professionals, who we can recommend. If you have a tradesperson, who you trust, we can support him/her. You can find our installation instructions and tips here.
Got a technical question?
All our technical data sheets are here. Your regional Texaa business representative can also help; please feel free to contact him/her.
Can I have an appointment?
Our business representatives travel every day to installation sites and to see our customers. Please feel free to contact them and suggest the best dates and times for you, preferably by e-mail.
Lead times
Our products are manufactured to order. Our standard manufacturing time is 3 weeks for most of our products. Non-standard products take from 5 weeks. We also perform miracles on a regular basis! Please feel free to contact us.
Who should I call?
To get a quote, a delivery time or technical information, we recommend you call your regional Texaa business representative, who you can find here.
Order tracking
If you need information about your order, please contact the person in charge of handling it: the name is at the top left of your quote.