Texaa’s hallmark, our “DNA”, is without question Aeria, a sound transparent, knitted fabric produced in our workshops in Gradignan, Gironde. Neither hand nor eye are left indifferent by the unique way in which light plays over its texture, creating an irresistible urge to touch and caress it, as if in search of intimate, insightful confirmation of something sight cannot grasp without the palpable experience of touch.
Texaa’s Origins
in Textiles
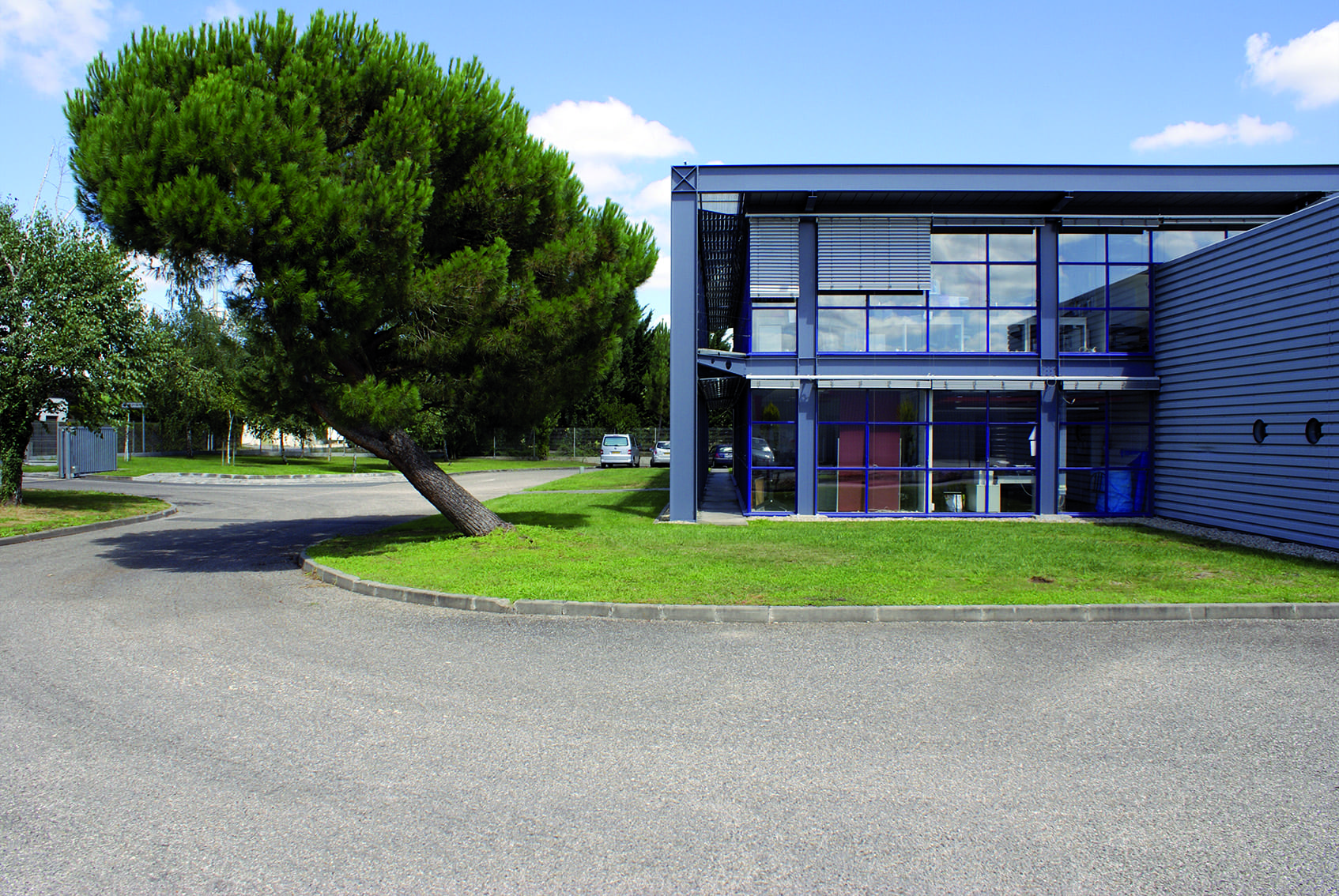
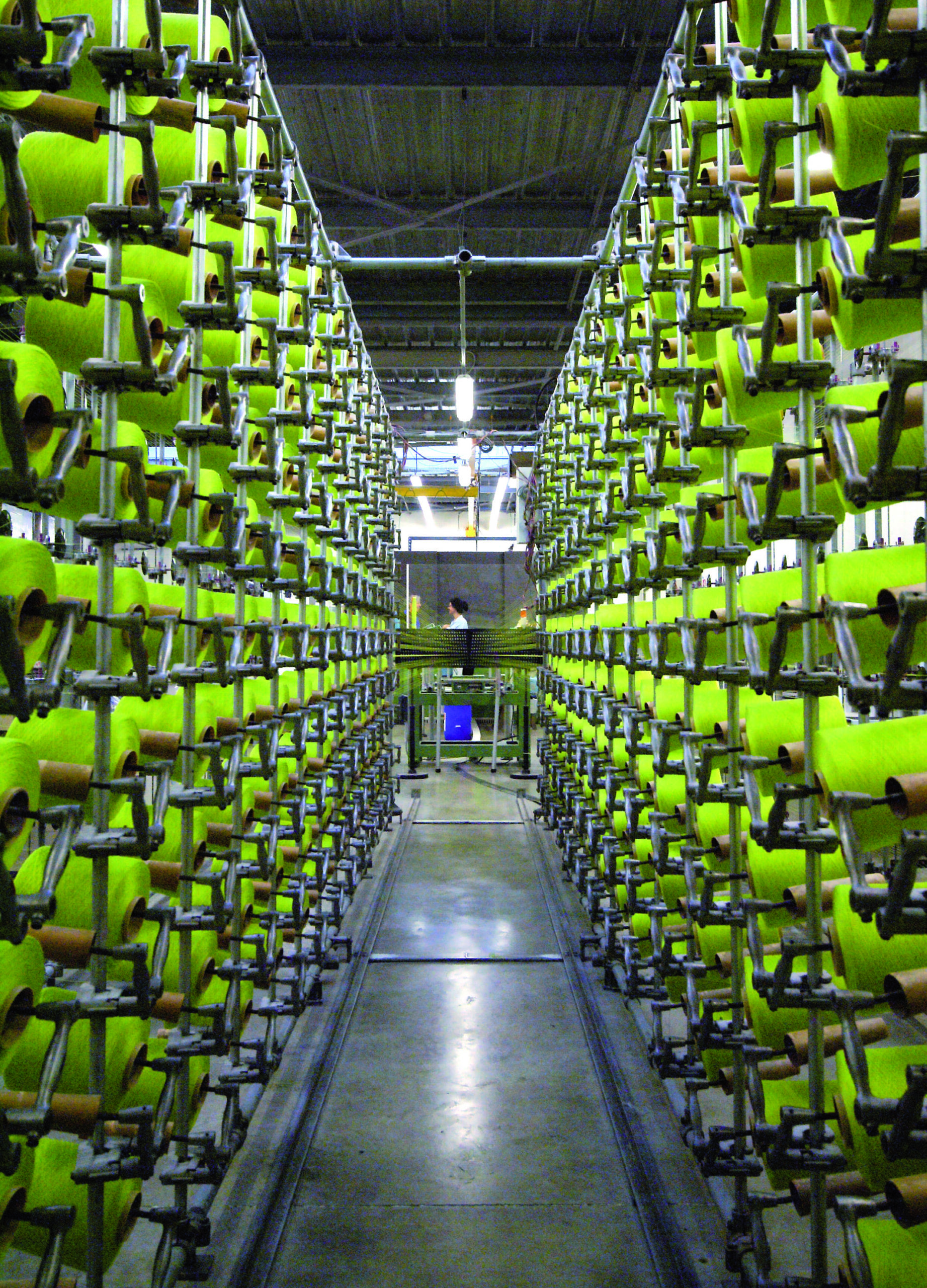
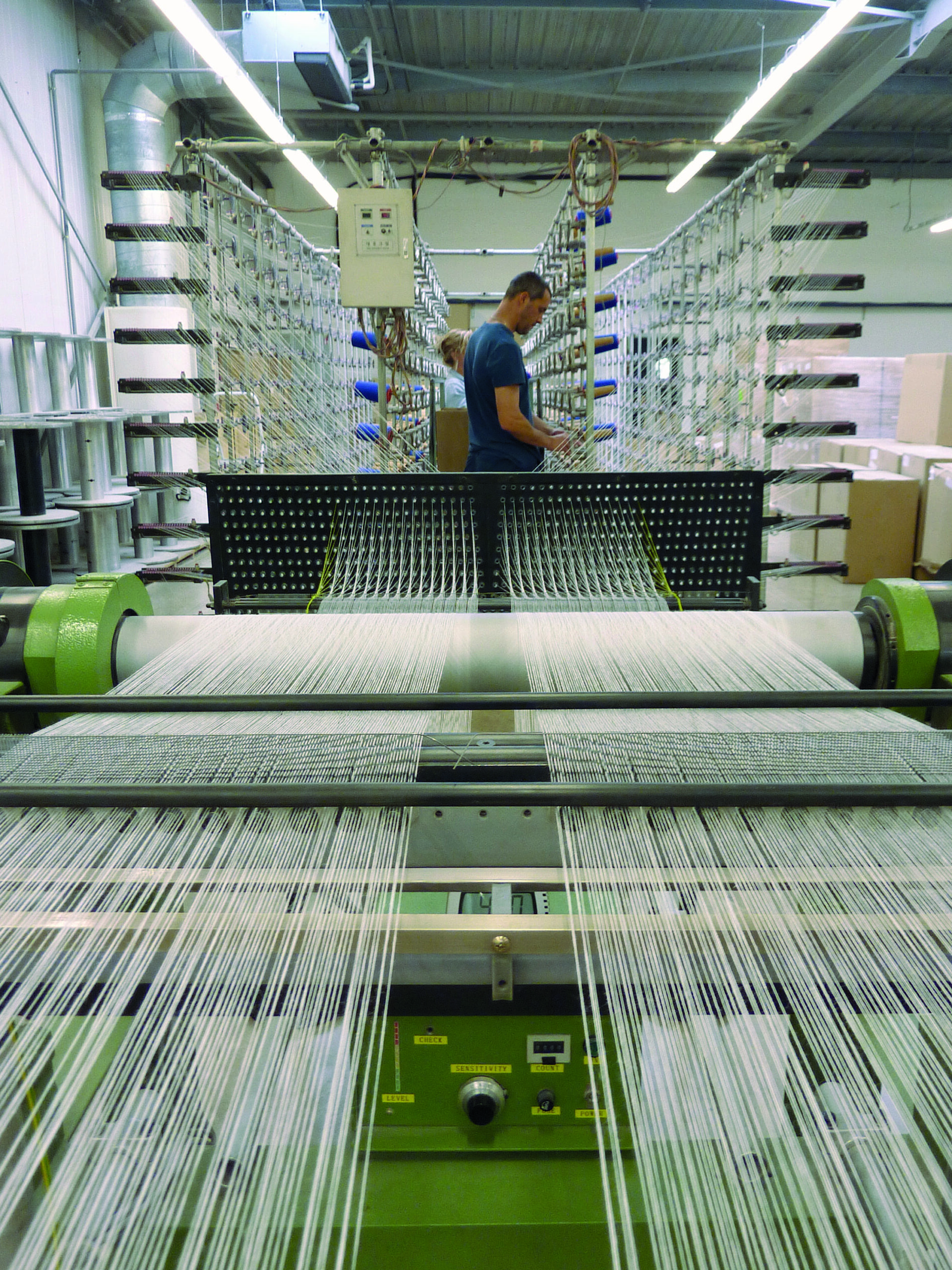
From textile workshop to building site…
A conversation with Bernard Demptos, on the choices and decisions which have shaped the company’s history and which continue to fuel the complex technical and industrial processes which first gave birth to Aeria, the unique material used in all Texaa products.
“The story of Texaa® began in 1979, the year I took over a well-known Bordeaux firm which had been making trimmings for over a hundred years—pompons and ribbons and the like—along with ‘open weft’, heavily sized textiles, like canvas, for the region’s slipper and sandal manufacturers. Just before I arrived on the scene, the firm had also been producing a series of light textiles, in a variety of weaves and yarns… As these fabrics were almost totally sound transparent, they had been laminated onto one of the first existing pliable foams to create ‘acoustic wall coverings.’ At the time, I knew virtually nothing about acoustics, but I had a sort of sixth sense that the firm’s specialist know-how could be used to great advantage in the building industry. So I let the trimmings side of its activity drop and concentrated on developing the acoustic textile side of things. Our main challenge was producing
a fabric that architects would find acceptable for their designs.”
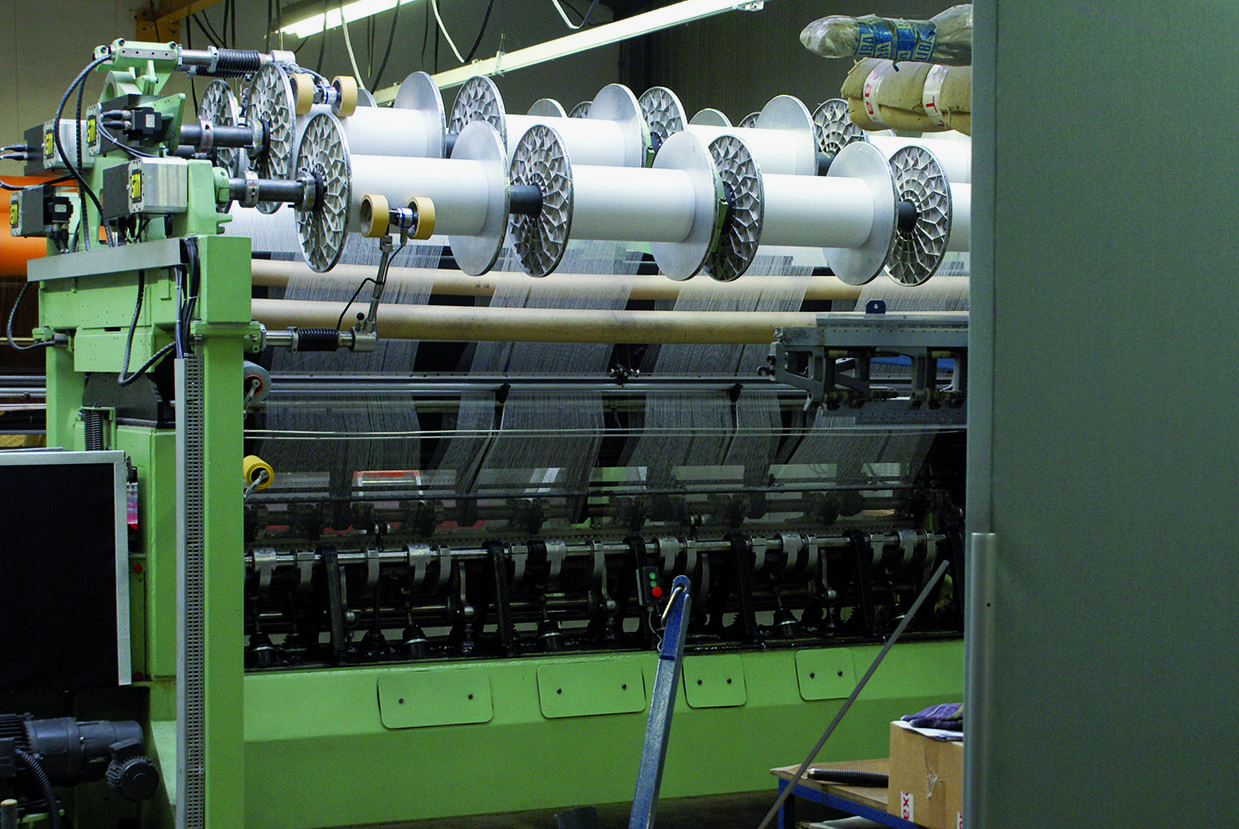
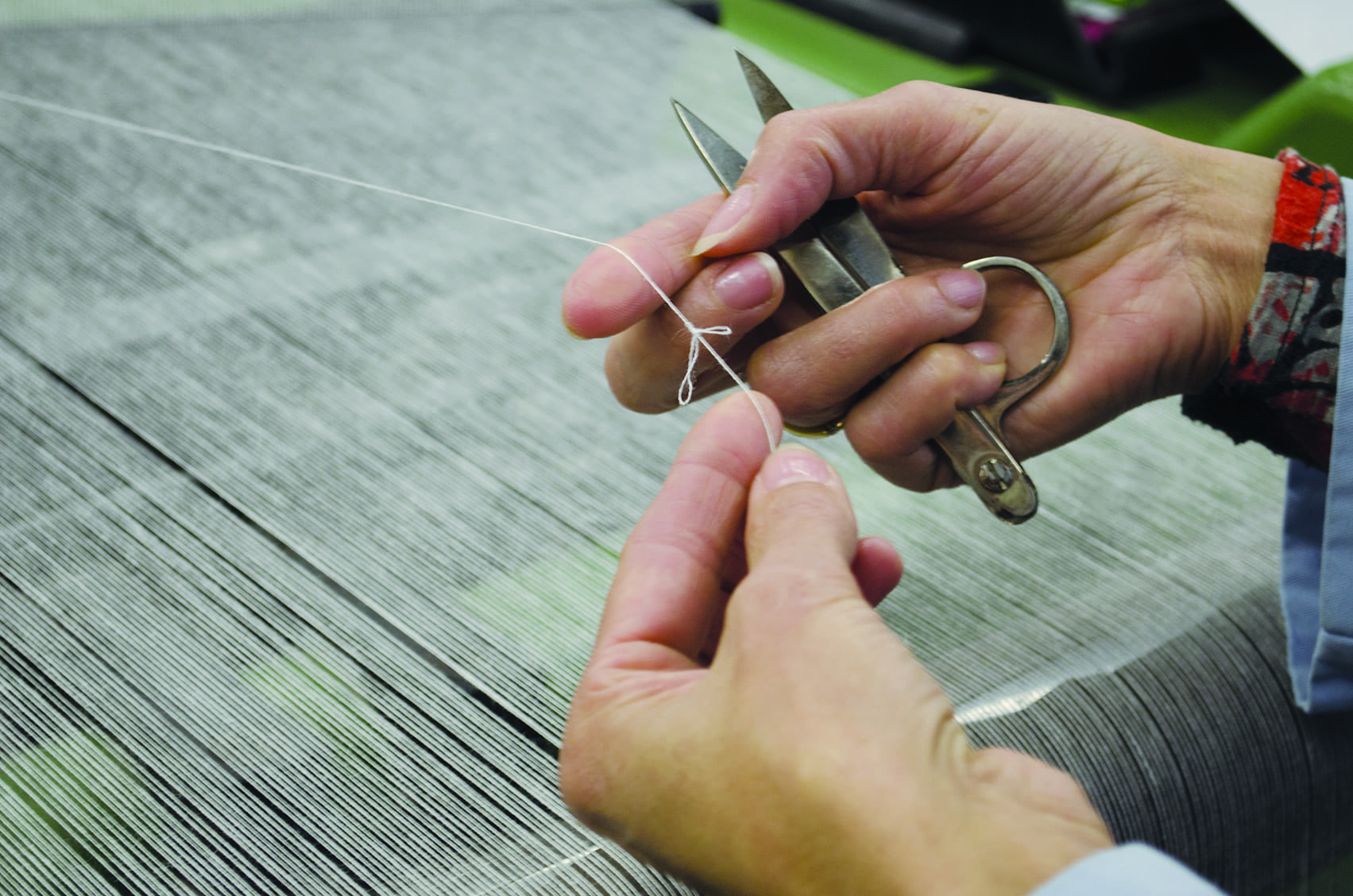
A stitch in time…
“To produce an open textured fabric whose shape may still be controlled, you have to find a means of positioning each thread at a regular interval, and this is not possible if you use a weaving technique. The only solution is to knot each thread to produce a mesh, like when you make a net. This is why my predecessors looked to knitting to produce the open textured fabrics required for use in sandal manufacturing. Guided by the educated eye of my good friend, plastic artist Daniel Dartois, I first plumped for what is called ‘moss’ or ‘seed’ stitch. The result was a resounding commercial failure and was soon dropped in favour of a ‘round’ stitch which—although revisited on many an occasion—is basically the same stitch we use today. The advantage it presents lies in its flexibility, the full benefit of which is reaped once it is associated with a pliable foam backing. Imagine the stress and strain the fabric is subjected to when laminated onto the foam (especially in the early days, when the latter was so thick), only then to be rolled into bales ready for transport. Thanks to our round stitch, the fabric doesn’t crease or tear, and it returns to its initial shape as soon as it is laid out flat. In certain instances, blinds, for example, we also use a ‘square’ stitch whose properties are diametrically opposed, i.e. the fabric does not lose shape… Once we had settled upon the round stitch, our research did not stop there, and a whole series of experiments and tests followed in relation to our knitting and sizing techniques. The result of all this is the fabric we now call Aeria, and it is without a doubt one of our most precious assets.”
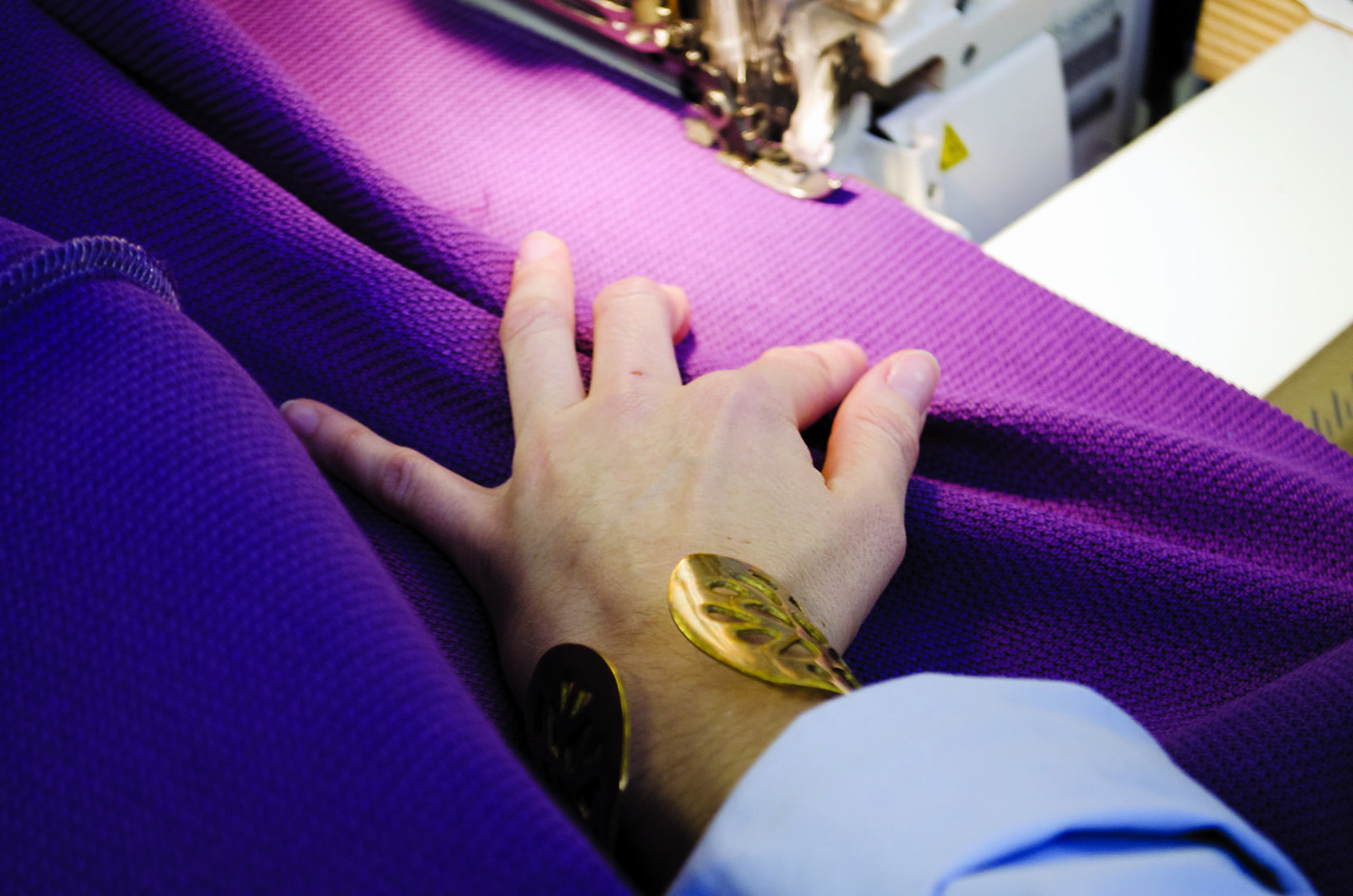
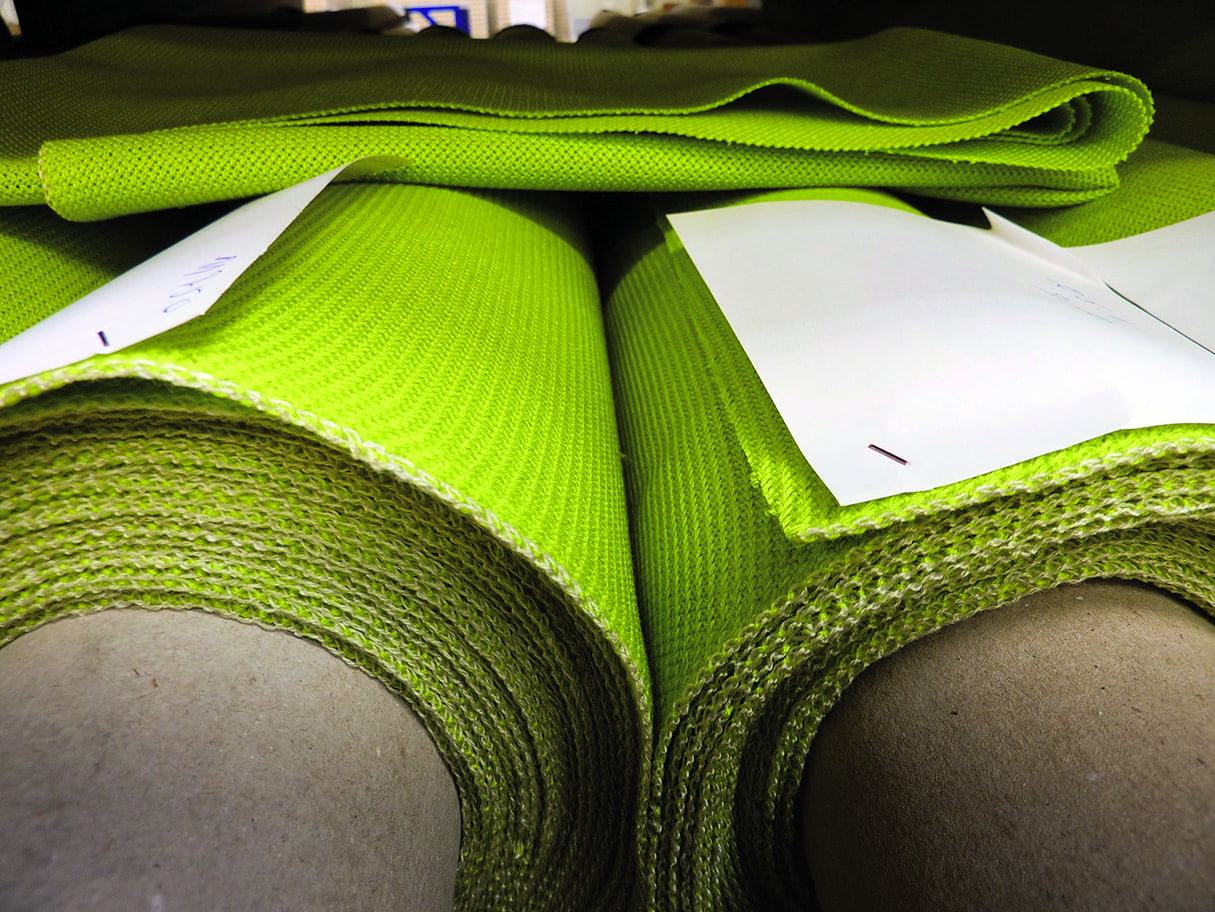
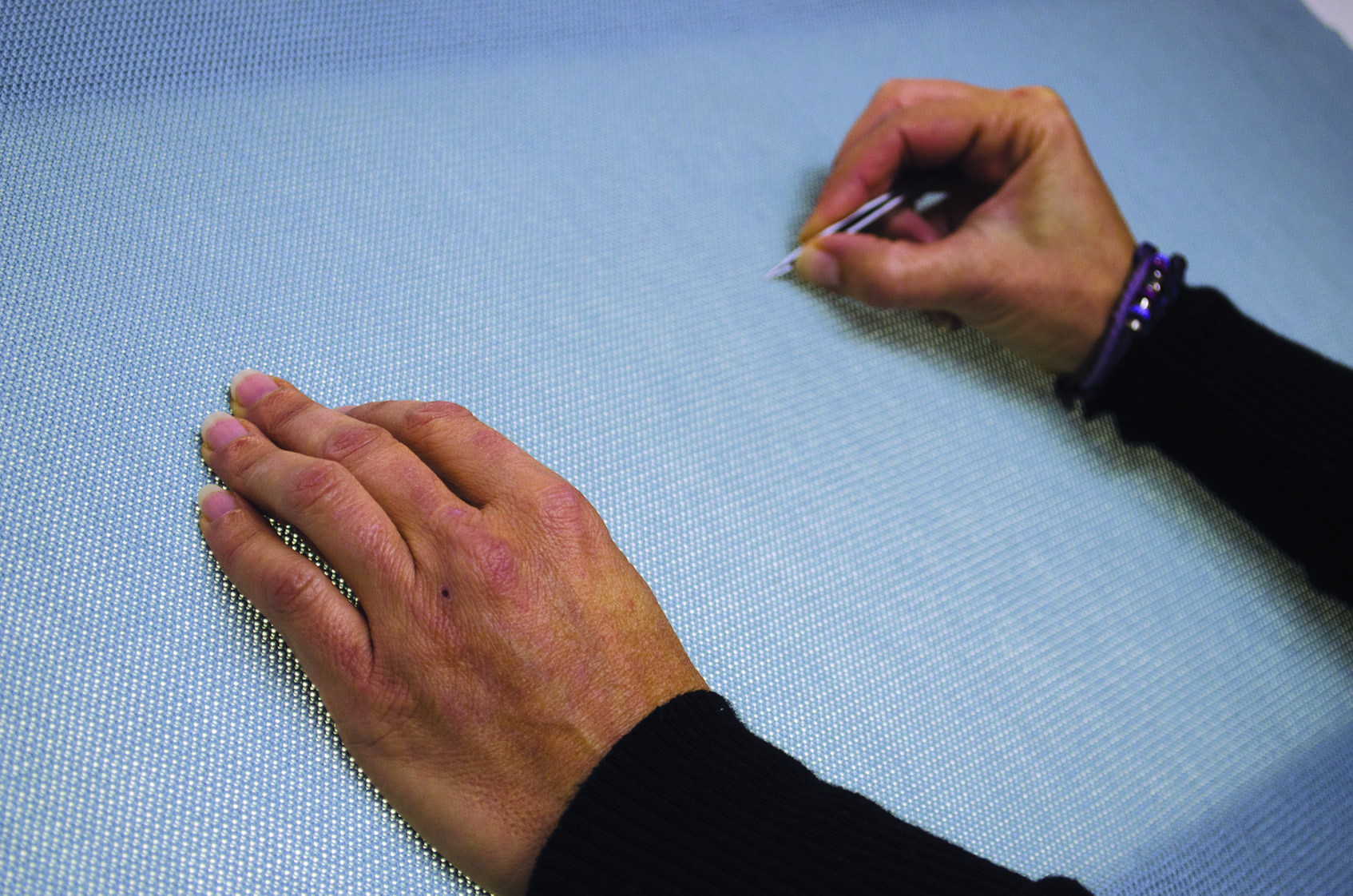
The chemistry of materials
“The raw material we work with is fibre, a fibre selected with the greatest care, after lengthy testing. This fibre requires the utmost care in handling. Spinning, in particular, must be carried out at an unhurried pace.
In addition to this, new norms are constantly being introduced, affecting the composition of the substrates and resins we use. We test all new fibres produced worldwide, sometimes even before they are commercialised, and our research centres not only on the new fibre per se, but also on its interaction with other materials. This is also true for foams and we work in close partnership with our suppliers. We always prefer products which will neither melt nor drip if exposed to fire, whether standard regulatory tests provide evidence of this or not. These factors stem from the chemical composition of the materials used, and our know-how in this field is a key force—it would not be easy to reproduce the diverse qualities of the products we make.”
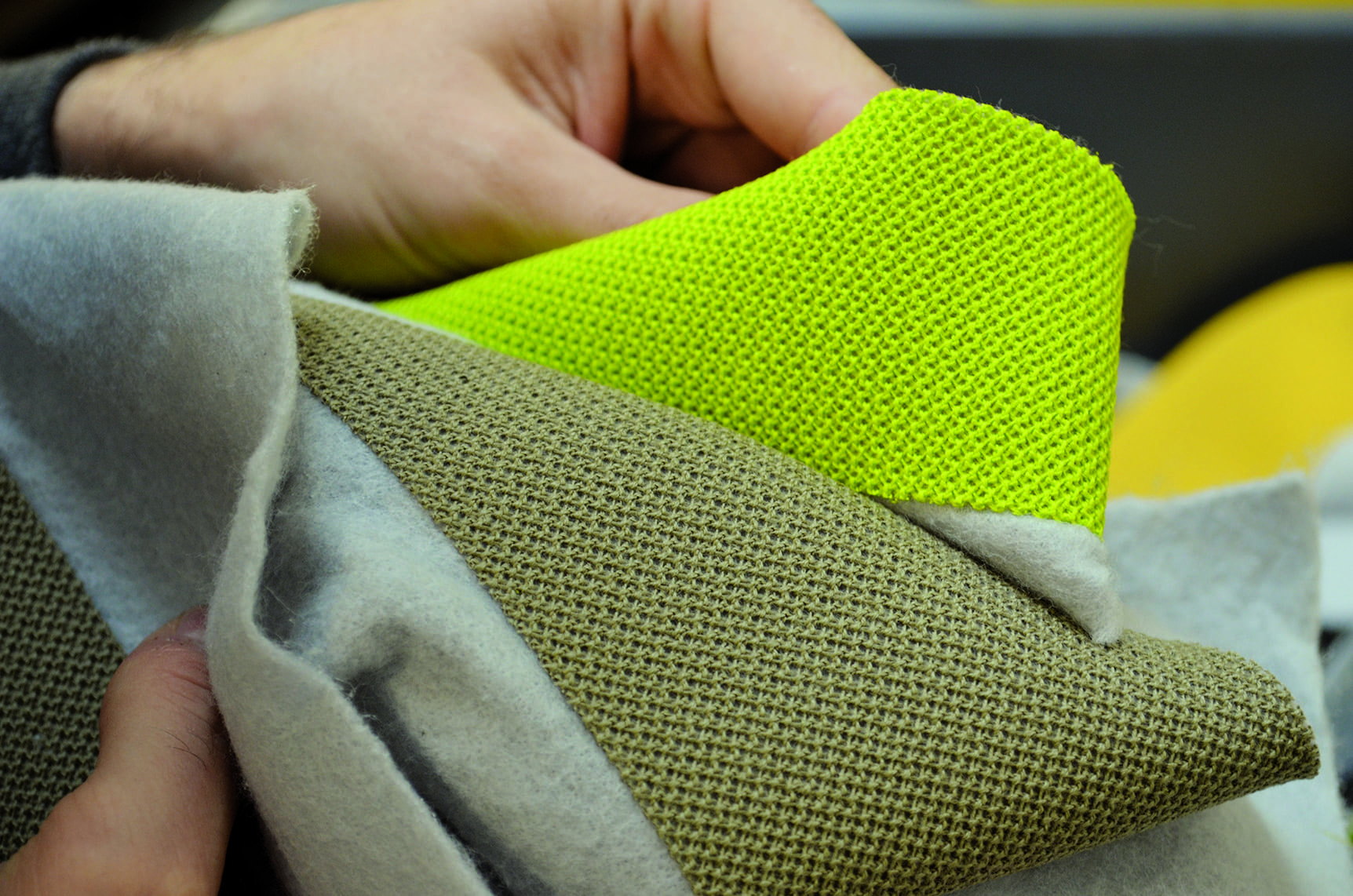
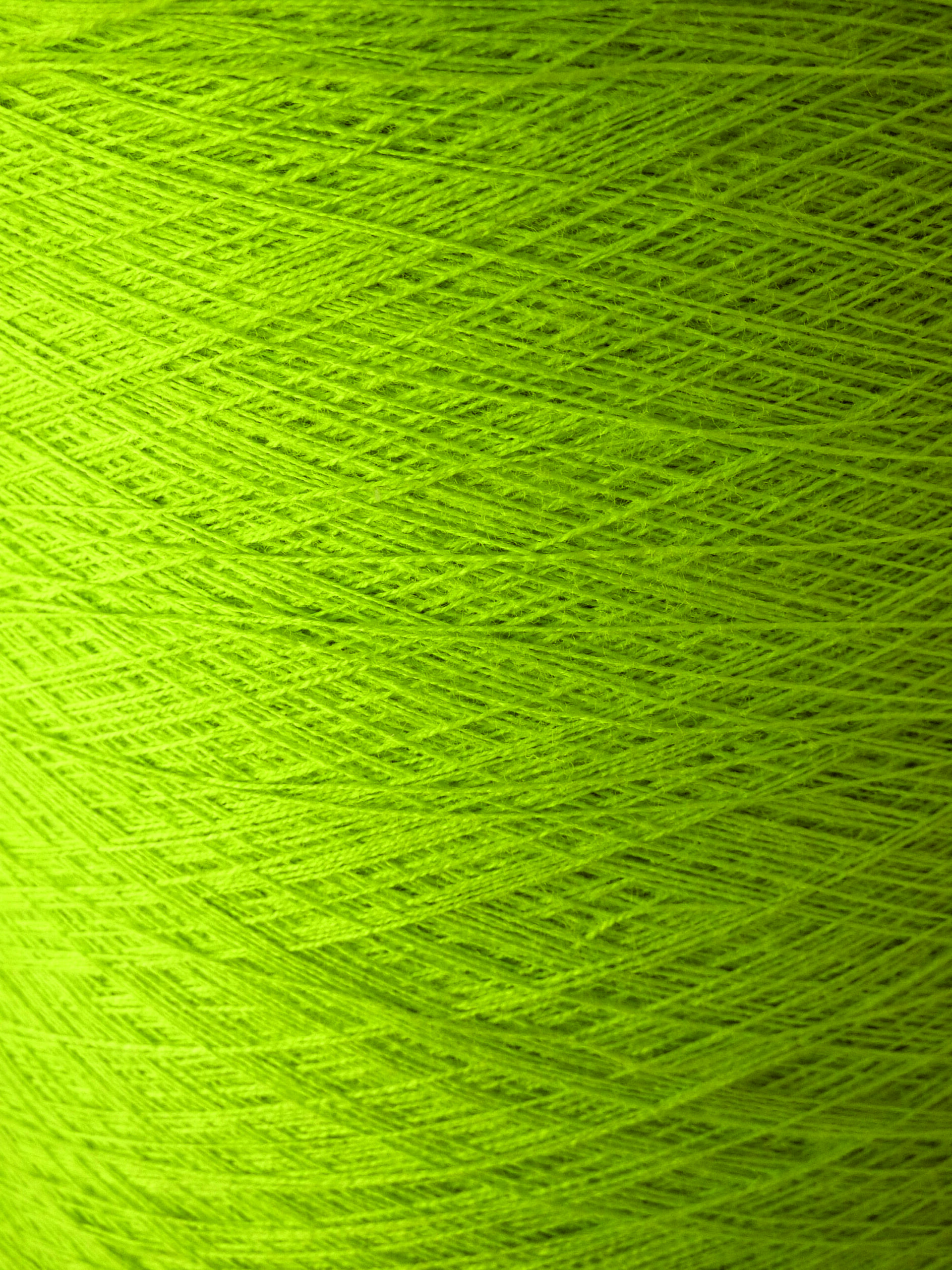
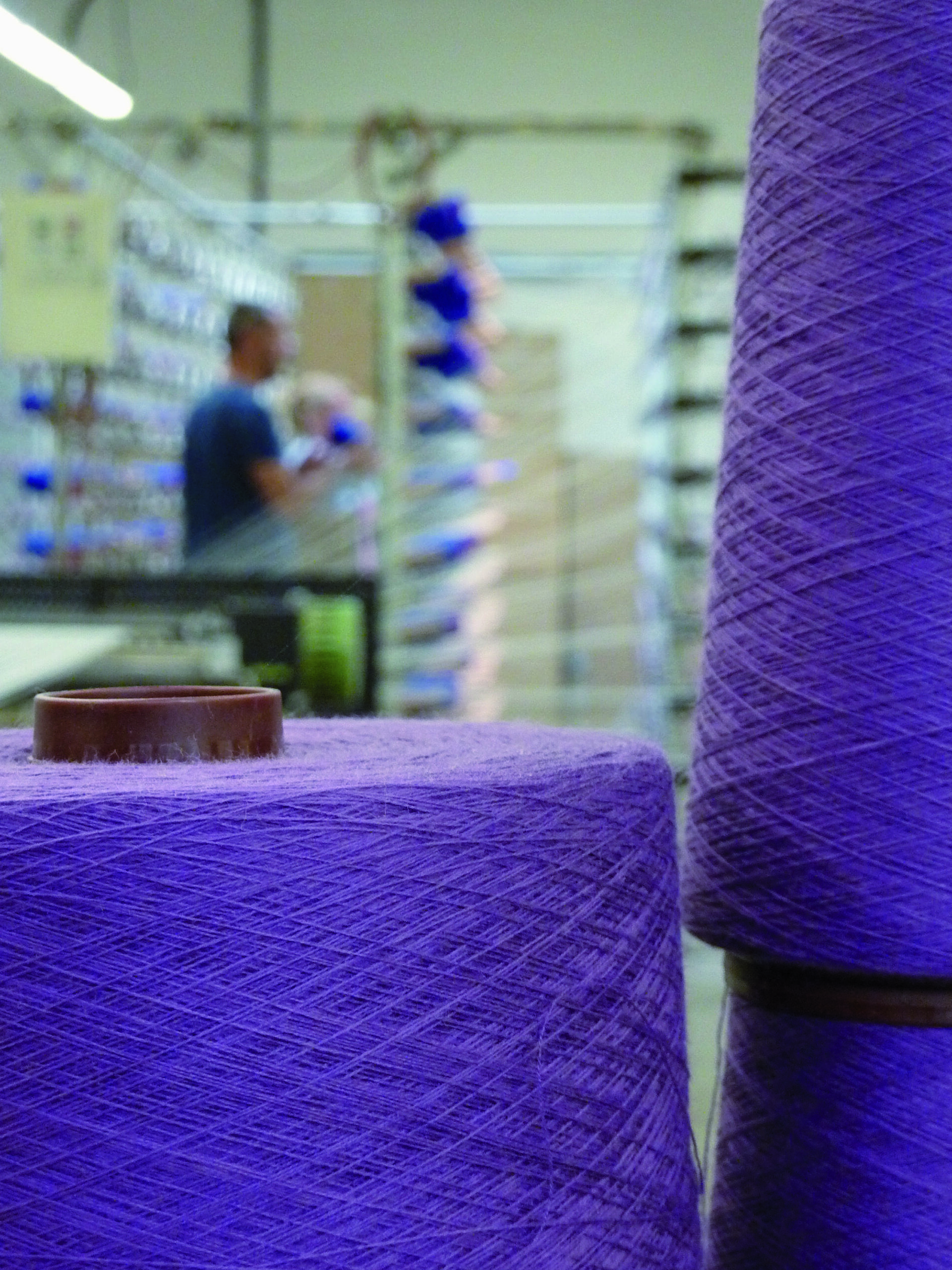
From textile workshop to building site
“Our first line was a range of wall coverings on which the company thrived for about ten years. During this phase of Texaa®’s gestation, we considered and indeed presented our products as if they were ‘wallpaper.’ And indeed they earned us a decent living. However, their acoustic qualities were self-evident, and, in the meantime, we had gained the trust of a number of engineering firms. There was no reason for us to stop producing the wall coverings, and we wouldn’t have had the means to do so anyway. But convincing architects to use them was quite a different matter. They had no real desire to use our products, and only did so when there was no other alternative available. This was a particularly difficult time – we knew that our know-how had its uses, but those uses were unquestionably limited. So, we went back to the drawing board and embarked on more research, re-examining the quality of our fabric, the stitching we used, the cloth’s texture and grain. We began to design panels and stretched screens on frames, followed by acoustic objects in a variety of shapes (cones, cubes, bricks, etc.), exploring the principle of acoustics through objects as a complement to treating the surface of a given space. With the help of architect and colourist Christine Bernos, we abandoned the palette of our early days and developed a range of colours designed to appeal to architects.
We also turned our attention to more practical questions, systems to fix our products into place, their fitting and finishing if you like, and we set out to devise technical solutions for the problems encountered in situ on the building site. This led us to exchange with the trades concerned and to set up training courses for those who wished to specialise in installing our products. Today, our Vibrasto range—in either its ‘stretch and anchor’ or ‘stretch and glue’ version—is popular among the up and coming generation of young architects and interior designers. They see a substance and warmth in our textiles, a colour palette and grain offering an exciting and efficient means of addressing the question of acoustic comfort. This is a source of great joy and pride.”
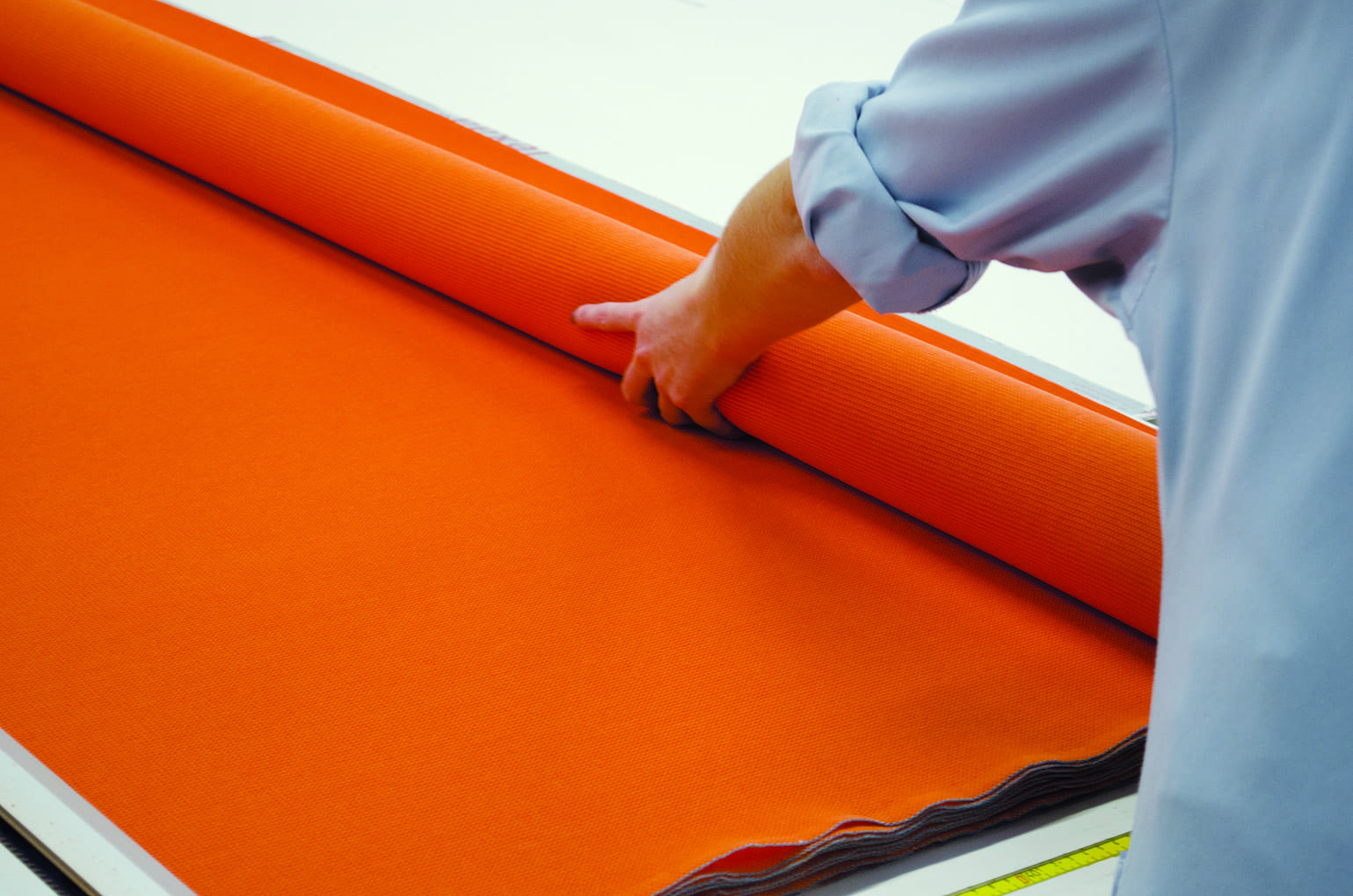
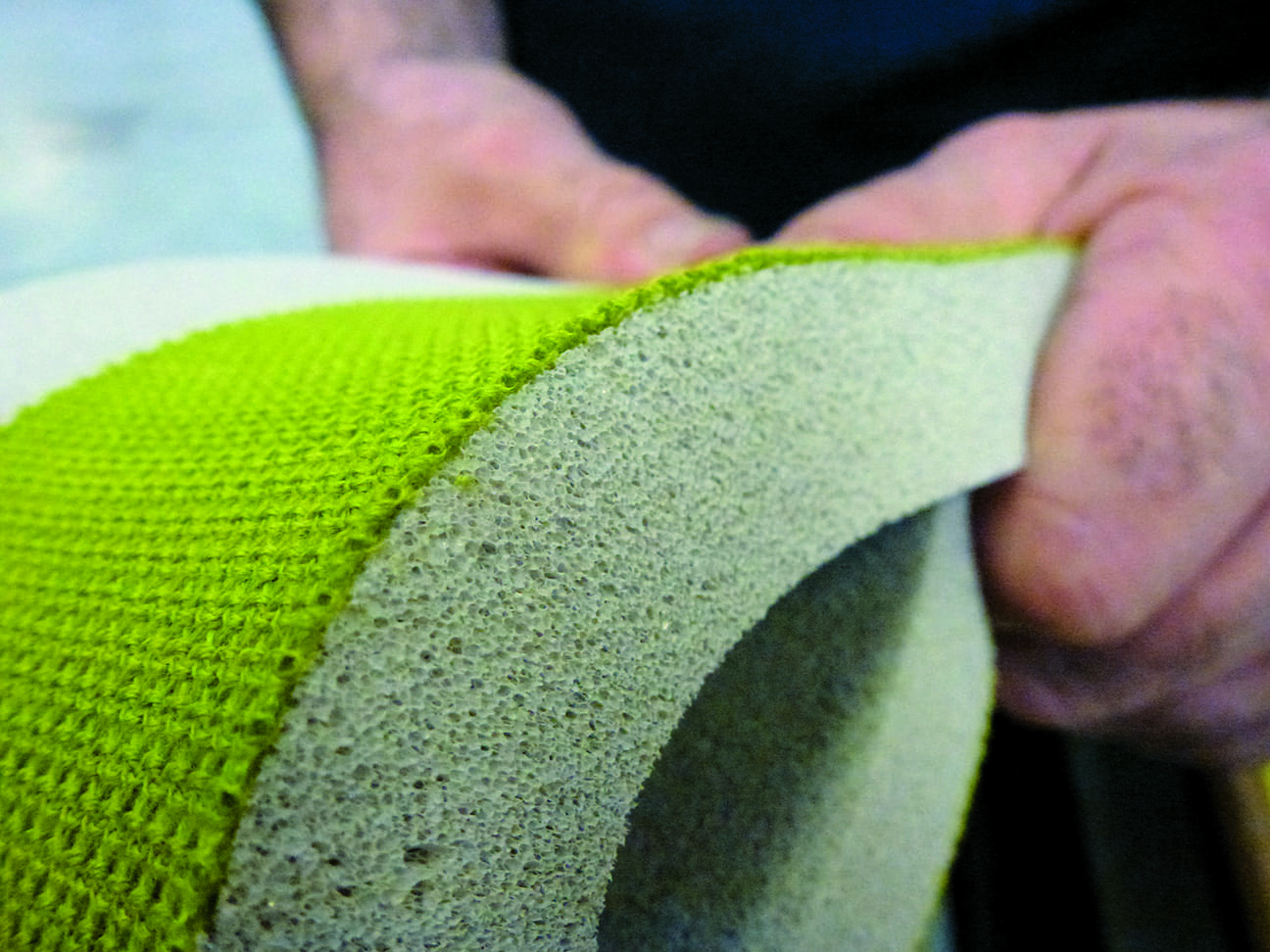
Partaking in the pleasure of a job well done
“When I look back today on how far Texaa® has come, it seems quite clear that our most important decisions have been conditioned by an ambition shared with almost all those involved in our making. The ambition to grow a successful business, of course, but not that alone. Our true ambition has always been to partake in the pleasure of quality achievements. Be they great or small.”
How can I get a quote?
By contacting the Texaa business representative of your region by telephone or e-mail and leaving your contact details and what you need. We will send you a quote promptly.
How can I order Texaa products?
Our products are manufactured in our workshop and made available to order. Just contact the Texaa business representative of your region. If you already have a quote, you can also contact the person handling your order: the name is at the top left of your quote.
How do I get my products installed?
Joiners and upholsterers are the best skilled to install our products easily. We work regularly with some professionals, who we can recommend. If you have a tradesperson, who you trust, we can support him/her. You can find our installation instructions and tips here.
Got a technical question?
All our technical data sheets are here. Your regional Texaa business representative can also help; please feel free to contact him/her.
Can I have an appointment?
Our business representatives travel every day to installation sites and to see our customers. Please feel free to contact them and suggest the best dates and times for you, preferably by e-mail.
Lead times
Our products are manufactured to order. Our standard manufacturing time is 3 weeks for most of our products. Non-standard products take from 5 weeks. We also perform miracles on a regular basis! Please feel free to contact us.
Who should I call?
To get a quote, a delivery time or technical information, we recommend you call your regional Texaa business representative, who you can find here.
Order tracking
If you need information about your order, please contact the person in charge of handling it: the name is at the top left of your quote.